2015-04-24 Product news
Alfa Laval introduces biggest Diabon® plate heat exchanger yet for corrosive applications
The latest addition to Alfa Laval’s Diabon plate heat exchanger portfolio is the largest unit ever built. Like all Alfa Laval Diabon plate heat exchangers the new Diabon S15 type is suitable for handling highly corrosive fluids. The impressive new heat exchanger will more than double flow rates. Therefore, a single Diabon S15 can replace shell-and-tube or block heat exchangers to provide all the familiar benefits of plate heat exchangers: for example, maximized heat recovery, minimized downtime and low maintenance costs, all of which add up to low operating costs.
Unique solution for corrosive environments
Alfa Laval worked with SGL Group to develop Diabon plate heat exchangers. They combine the high-efficiency heat transfer benefits of conventional plate heat exchangers with the exceptional corrosion resistance of Diabon graphite material. The Diabon S15 employs Diabon, a dense, synthetic resin-impregnated high-quality graphite with a fine and evenly distributed pore structure. It provides performance similar to the material used in SGL´s graphite blocks and graphite shell-and-tube heat exchangers and is suitable for use with corrosive media up to 200°C (390°F).
Diabon S15 can replace shell-and-tube or block heat exchangers
Previously, to get all the advantages offered by Diabon plate heat exchangers, customers sometimes needed several smaller units to replace one shell-and-tube or block heat exchanger. This is no longer the case. The new, bigger Diabon S15 can replace one or several shell-and-tube or block heat exchangers. In addition, fewer units provide the benefits of less pipework and lower installation costs.
Maximum heat recovery
In the Diabon S15, a combination of high turbulence and counter-current flow offers maximum heat recovery, which in turn allows significant energy savings. The principle is simple. Two media flow through channels between corrugated plates, creating a high degree of turbulence in the media. This results in better heat transfer between the media. A counter-current flow enables crossing temperature programs, where the cold fluid can be heated to temperatures very close to those of the hot fluid. The closer the temperature approach between two fluids, the more heat is recovered.
Less maintenance, more uptime and a long lifetime
The Diabon S15 is engineered to considerably reduce the need for maintenance, cleaning and service. A special plate pattern enhances turbulence, which means less fouling and thus less maintenance. The plates are also easily accessible and can be cleaned when needed with hydroblasting or with an automated cleaning in place (CIP) system. In addition, due to the outstanding corrosion resistant characteristics of Diabon graphite plates, there is rarely a need to stop operations to replace or repair components. Even in the harshest environments these materials maximize uptime and provide a long life cycle.
More to discover
Please visit Alfa Laval, in Hall 4.0, stand D4 at ACHEMA, Messe Frankfurt, Frankfurt am Main, in Germany June 15-19 2015.
태그:
모두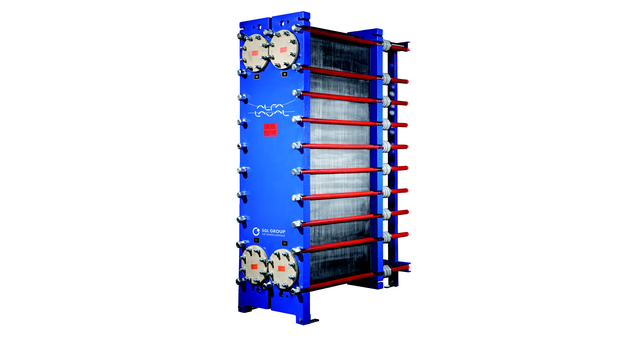