Perks of the job: Spanish coffee producer achieves dramatic drop in water use with Optiwia™ water-saving technology from Alfa Laval
As the EU continues to strengthen its regulations on water use in food production, many companies across Europe are working hard to understand their water risks and incrementally improve their water footprint. Companies focus on reducing the amount of water needed in their processes – increasing overall efficiency of water needed for cleaning and cooling, recovering and reusing as much water as possible and adequately treating wastewater for reuse or replenishment of local watersheds.
DATE 2025-05-12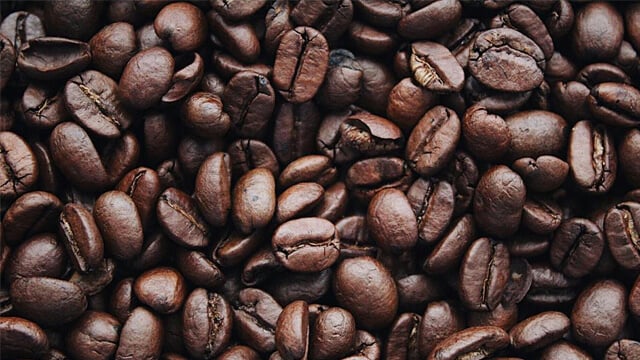
This is a demanding task, particularly for coffee manufacturers, as coffee production is very water intensive. In fact, the UN estimates that it takes 140 litres of water to grow, process, and transport enough coffee beans for just a single cup (UN).
Together with Alfa Laval, one coffee producer in Spain has significantly reduced its overall water consumption and is now saving thousands of litres of water every day by reusing cooling water previously lost to the drain.
Founded in 1998, Prosol produces more than 13 million cups of coffee and coffee products a day and exports them to more than 30 countries around the world from its manufacturing facilities in Palencia, in the Castile-León region of northern Spain.
A signatory to the UN Global Compact and with a strong focus on sustainability and circularity in its operations, the company identified significant potential for improvement in the amount of water used separation phase of the coffee production process where disc-stack centrifuges are in use.
“We have always promoted sustainability,” explains Francisco Javier Cantero, technical and process manager at Prosol. “And today, it’s not an option: It’s a responsibility. Joining the Global Compact and promoting the Sustainable Development Goals is a major step towards improving the future of everyone.”
At the time the company was scrutinizing potential water-reduction measures at its Palencia plant, 240 litres of fresh water every hour were going straight down the drain after completing the job of cooling the high-speed separator. This amounted to a total of 5,700 litres a day.
So, as part of their drive towards reducing this high level of water consumption, Prosol reached out to Juan Miguel Comillas from Alfa Laval’s Global Technology Business Development in BU High Speed Separators. As luck would have it, the team was in the process of developing new technology – specially adapted for applications with cold media, such as brewery, beverage and dairy processes and now called Optiwia – that could recover this cooling water for reuse.
Following testing during 2021-2022, the final commercial product was installed for use in 2024.
“The Optiwia technology means that Prosol can recover the cooling water and use it to flush the machine after every discharge,” Juan Miguel explains. “Before, it was going to waste, but now, we are collecting it in a tank and reusing it.”
Every day the company reuses the entire amount of recovered water of 5,700 litres - 2,040 litres are used in flushing, while the remaining is used as a cooling water supply, says Juan Miguel.
“They are very happy at Prosol, and we now know that with Optiwia, food & beverage producers can save up to 70% of the total water consumption, and we can confidently say to the market that we supply the perfect centrifuge for all cold food applications with respect to water.”
Optiwia™: 물 효율성을 위한 업그레이드
알파라발의 Optiwia™는 음료 생산 분리기를 위한 독립형 플러그 앤 플레이 물 절약 업그레이드로 물 소비량을 최대 70%까지 줄이도록 설계되었습니다. Optiwia는 냉각을 위해 물을 재사용함으로써 비용을 최소화하고 효율성을 향상시키며 지속가능한 음료 생산을 지원합니다. 제어 시스템에 연결할 필요가 없어 설치가 간편하며, 일정한 수압을 보장하고 효모 배출 문제를 해결합니다. 더욱 스마트하고 친환경적이며 비용 효율적인 음료 공정을 위해 Optiwia로 업그레이드하세요.
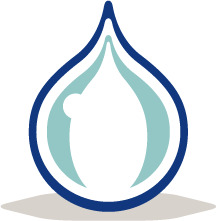
Optiwia™ enables for savings of up to 70% of the total water consumption for the centrifuge.
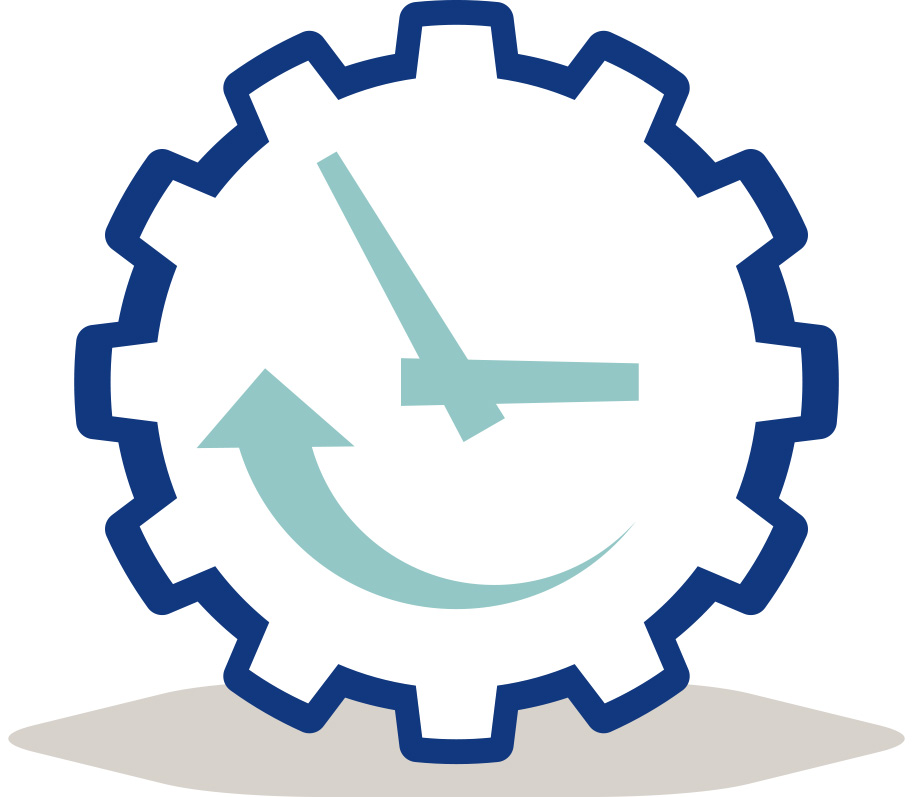
Due to droughts over recent years, the uninterrupted water supply is increasingly a factor to consider in safeguarding the maximum uptime of food and beverage processing lines on the Iberian Peninsula.